Brushless-Motor wickeln
(fertiggestellt Sommer 2011)
Nachdem ich aufgrund von erneutem "Baubedarf" und Dusslichkeit bei der Ersatzteilbeschaffung gerade mit dem Kopter sowohl Flug- als auch Baustopp habe, werde ich meine Fotodokumentation einer vergangenen Hardwarerettung mal vostellen.
Worum geht es? Die Motorwicklung eines Brushless-Motors zu erneuern.
Gleich vorweg:
- Das macht ist viel Arbeit.
- Es kostet mehr Zeit als Geld.
- Ob sich das lohnen kann, sollte vorher evaluiert werden.
- Diese Anleitung ist zum Nachahmen nicht hinreichend.
- Eine ausgiebige Lektüre von powercroko zum Bewickeln ist zwingend erforderlich: http://www.powercroco.de/Bewickeln.html
0 Lohnt es sich anzufangen?
0.1 Liegt der Fehler überhaupt in der Wicklung?
- Ein Symptom ist, dass die Motoren unter Strombegrenzung nur kurz anlaufen oder gar nicht erst starten (intakter BL-Ctrl vorausgesetzt)
- Widerstand zwischen den Motorpolen untereinander und mit einem gesunden Motor vergleichen!
- Auf Kurzschluss mit Statorblechen prüfen!
- Geschmolzener Lack an den Wicklungen?
0.2 Machbarkeit
- sind die restlichen Bauteile in Ordnung? Es bring nichts, wenn der ganze Motor Schrott ist.
- Ist nichts verbogen, die Lager in Ordnung, die Achse noch gerade?
- Läuft die Glocke noch auf einem intakten Stator? Wenn durch die Hitze, die die Wicklungen kurzgeschlossen hat, die Magnete auch gelitten haben, bringt das alles nichts.
0.3
- Habe ich die Zeit?
0.4
- Kann ich mich mit 5-20 % Leistungseinbußen oder Strom-Mehrverbrauch begnügen?
Ja? Dann los!
1 Auseinander bauen
Bild 1: Motor ohne Glocke
Bild 2: Schnipp-Schnapp-Kabel ab
Bild 3: Bei 100°C den Kleber aufweichen
Bild 4: Schnell einspannen und mit 2 Schraubenziehern das Lager mit sanfter Gewalt aus dem Stator hebeln
Bild 5: Topflappen fetzen übrigens bei 100 °C
Bild 6: Ofen wieder ausmachen spart immens viel Strom
2 Alte Wicklung raus
Das Abwickeln der verklebten Drähte sorgt für Frust. Deswegen sollte man gleich mit Werkzeug zur Tat schreiten. Ganz Wichtig: Eine Wicklung unbeschädigt stehen lassen, um die Anzahl der Windungen zählen zu können.
Bild 7: Einspannen und dem ganzen mit dem schmalen Eisensägeblatt auf den Leibe rücken.
Bild 8: Das macht übrigens Dreck
Bild 9: Seitlich die Wicklungen auftrennen
Bild 10: Und dann kann das Gefummel losgehen. Ich wünsche jedem Nachahmer Nerven wie Drahtseile
Bild 11: Ein billiger Uhrmacherschraubenzieher kann verklebte Wicklungen trennen oder durch die Lücke schieben. Dieser ist aber am Ende unter Umständen kaputt (juhu, mehr Werkzeug kaufen)
Bild 12: Strick reinigt den Stator in der Mitte
Bild 13: und an den Stirnseiten
Bild 14: ta-daaa fertig demontiert.
Bild 15: Am Ende ist erst mal aufräumen angesagt.
3 Stator isolieren
Wer schon einmal den Effekt von bewegtem Metall auf Lack beobachtet hat, sieht ein: Eine Stelle ist auf jeden Fall kaputt. Deswegen sollte man sich in Schritt 2 nicht ewig aufhalten sondern lieber einen Pinselstrich mehr machen. Hauptsache ist: Die Farbe ist nicht zu spröde und nicht leitend. Am Ende muss natürlich alle Farbe an den blanken Außenseiten wieder runter. Sonst schleift die Glocke.
Bild 16: Stator isolieren
4 Jetzt wirds spannend: Wickeln
Wenn man aufgepasst hat, weiß man:
- Wieviele Windungen waren drauf? (parallele Leitungen zählen nicht)
- Wie viel Querschnitt gabs pro Windung? (parallele Leitungen zählen)
Bei den abgebildeten Motoren waren das 4 Adern à 0.2 .. 0.25 mm Durchmesser (mit Lackschicht) pro Wicklung, 15 oder 16 Wicklungen. Ich hab stattdessen 15 Wicklungen 0.35 mm² aufgezogen.
Das passende Wickelschema gab es beim Powercroco, der inzwischen nicht mehr öffentlich ist. Er empfiehlt aber eine andere Webseite, die das wissen noch bereit hält: http://lambertus.info/.
Das einzige allgemeine zur Wickeltechnik: nichts als Zughilfe benutzen. Einmal verkehrt gewickelten Draht weghauen und neu beginnen, da man nicht sieht, wie viel länger der jetzt ist und ob die Isolierung gelitten hat.
Bild 17: Vorbereitung
Bild 18: Schema ausdrucken und den Stator beschriften
Bild 19: Lange Enden stehen lassen und immer von der Spule abwickeln (nicht vorher abschneiden)
Bild 20: Und immer gleich sofort andrücken (nach jeder halben Wicklung, mit etwas Erfahrung auch erst nach jeder ganzen). Die Wicklungen müssen dicht liegen, sonst passen sie nicht rein. MITZÄHLEN (wobei man mit einem Zahnstocher auch nochmal nachzählen kann) und
RICHTUNG BEACHTEN
Bild 21: Einmal hin, einmal her, ...
Bild 22: rundherum, das ist nicht schwer.
Bild 23: Alle Wicklungen sollten die gleiche Struktur haben (hier z.B. innere Lage neun Windungen hoch, äußere Lage sechs Windungen runter)
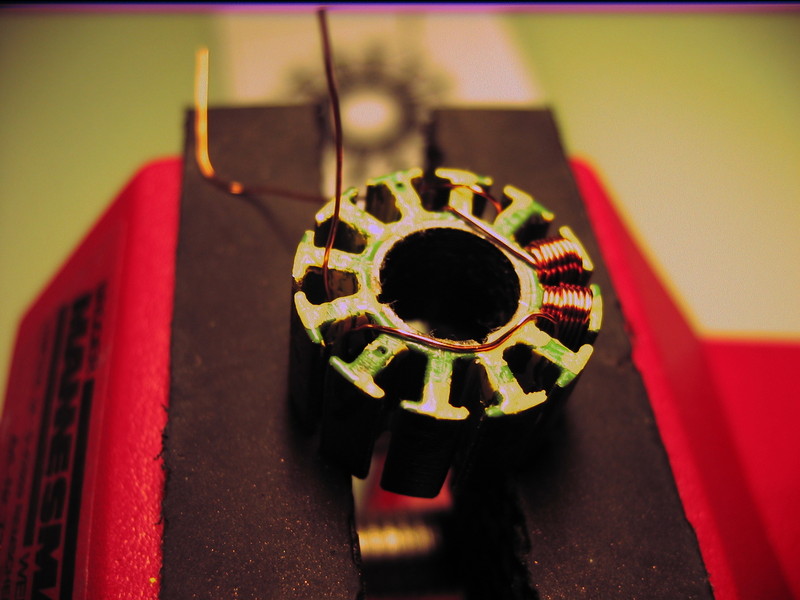
Bild 24: Genügend Draht am Übergang lassen, sodass des Gehäuse mit den Lagern wieder durchpasst.
Bild 25: Puh war das schwer... nur noch 2 Mal dafür mit weniger Platz.
Bild 26: Noch mal *zerknirschtguck*
Bild 27: DONE
Bild 28: Sieht besser aus als vorher.
5 Anschließen
Bild 29: Haben wir auch nichts vergessen? Dran-Schneiden geht nicht.
Bild 30: Verzinnen. Lötkolben auf volle Leistung und unbedingt die Wicklung auf der Motorseite kühlen (z.B. mit einer Zange).
Bild 31: Fertig!
Bild 32: Kabel dran. Auch hier das Kühlen nicht vergessen. Das ist ein heißer Tanz zwischen kalter Lötstelle und einem neuen Kurzschluss auf der Wicklung.
Bild 33: Alle dran.
Bild 34: Isolieren!
Bild 35: Kabel wieder ins Gehäuse einfädeln.
Bild 36: Tiefer!
Bild 37: Und schön GLEICHMÄSSIG und gemächlich und OHNE VERKANTEN das Gehäuse wieder durch den Stator pressen (das sollte schwer gehen).
Bild 38: Für das letzte Stück nimmt man etwas Küchenpapier und eine X-ziger Nuss.
Bild 39: Das macht einen schönen Abdruck und einen guten Eindruck.
6 Montage
Bild 40: Glocke wieder drauf!
Bild 41: Splint wieder dran!
Wie man leicht sieht, ist da auch noch ein weiteres Stück Schrumpfschlauch dazu gekommen
7 Testen
Ob die Motoren wieder anlaufen, bekommt man im Motortest auch ohne Propeller raus.
Die Leistungsaufnahme messen sollte man mit
- Last
- Kühlung
Bild 42: VERANKERUNG (zum Beispiel an einen schweren Buch festbinden ;) )
8 Ergebnisse
Das war mein erster Versuch und ich bin überrascht, dass es ging. Die Motoren ziehen bei gleichem Gaswert 10-20 % mehr Strom als die Originalwicklungen. Das könnte man mit etwas Rechnen und prüfen eventuell noch so deichseln, dass man die Wicklung mehr drauf macht, über die ich am Anfang spekuliert hab.
Ich schiebe den Mehrverbrauch übrigens hauptsächlich auf die Magnete, die durch die Hitze definitiv gelitten haben müssen.
Parameter zum Optimieren
- Windungzahl
- Querschnitt
- Litze (original) oder Draht (Reparatur)
Man sieht, das ist ein weites Feld.
Ich war eigentlich ganz froh, dass die Schleuder ohne immensen Finanzaufwand wieder flog. Dafür und für die Bastelei hat sich's gelohnt. Irgendwann bekommt der Kopter sicherlich trotzdem wieder neue Motoren.